Introduction
Selective Laser Sintering (SLS) printing has taken the world of manufacturing and design by storm. Among the various materials used in SLS, PA12 (Nylon 12) has emerged as a game-changer. In this blog post, we’ll explore the fascinating world of SLS printing and delve into how PA12 is revolutionizing industries, from aerospace to fashion.
What is SLS Printing?
Begin your portfolio journey by defining its purpose. Are you aiming to impress potential employers, win clients, or share your accomplishments with peers? Understanding your target audience and goals will shape the content and design of your portfolio.
SLS printing, or Selective Laser Sintering, is an advanced 3D printing technology that utilizes a high-powered laser to sinter or fuse powdered materials together. Unlike traditional 3D printing methods that require support structures, SLS can create intricate, complex designs with incredible precision, making it a go-to choice for industries seeking high-quality, functional parts.
The Advantages of SLS Printing
- Complex Geometry: SLS can produce complex, intricate designs that were once considered impossible.
- Material Versatility: A wide range of materials can be used in SLS, including plastics, metals, and ceramics.
- Reduced Waste: SLS is an additive manufacturing process, meaning it generates minimal waste compared to subtractive manufacturing methods.
- Speed and Cost-Efficiency: SLS is known for its speed and cost-effectiveness, making it ideal for prototyping and small to medium production runs.
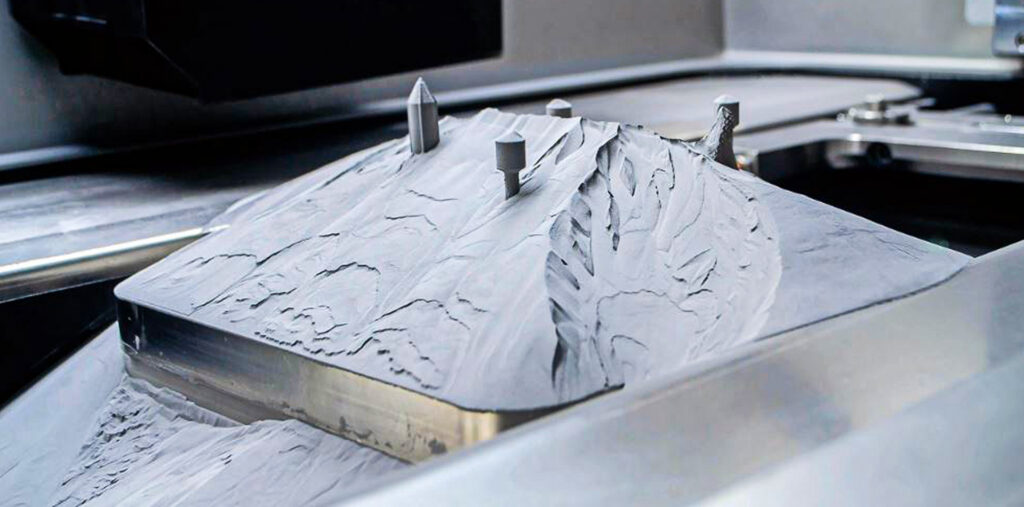
Enter PA12 Material
PA12, or Nylon 12, is a thermoplastic material known for its exceptional properties that make it perfect for SLS printing:
- High Durability: PA12 is renowned for its toughness and resistance to wear, making it suitable for functional parts that require strength and durability.
- Chemical Resistance: It is resistant to a wide range of chemicals, ensuring the longevity of printed parts in various environments.
- Temperature Resistance: PA12 can withstand high temperatures, making it ideal for applications in the automotive and aerospace industries.
- Low Friction: Its low coefficient of friction makes it suitable for applications where parts need to move smoothly.
Applications of SLS Printing with PA12
- Aerospace: PA12’s lightweight and high-temperature resistance make it a preferred choice for manufacturing aerospace components, reducing overall weight and fuel consumption.
- Medical Devices: SLS-printed PA12 is used to create custom medical devices and implants, ensuring a perfect fit for patients.
- Fashion and Wearables: The fashion industry is leveraging PA12 for creating avant-garde and functional clothing and accessories.
- Automotive: In the automotive sector, PA12 is used for prototyping, creating interior components, and even producing under-the-hood parts.
- Consumer Electronics: PA12’s excellent electrical insulating properties make it suitable for various consumer electronic applications.
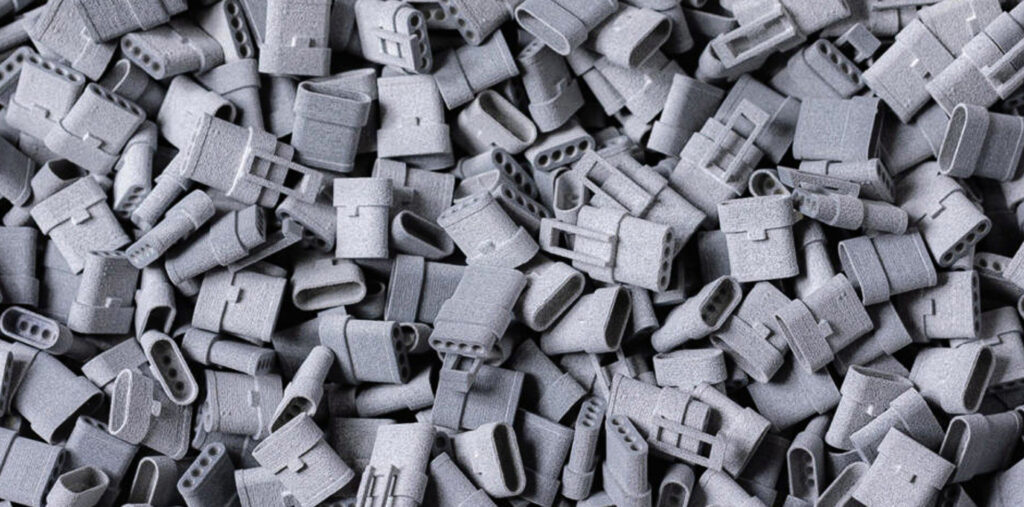
The Future of SLS with PA12
As technology advances, we can expect to see even more innovative applications for SLS printing with PA12 material. Its ability to provide cost-effective, high-quality parts with unparalleled design freedom positions it as a cornerstone of future manufacturing and design processes.
In Conclusion
SLS printing with PA12 material is a transformative force in various industries, pushing the boundaries of what’s possible. Its versatility, durability, and precision have opened up new avenues for designers and manufacturers to create functional, complex parts that were once mere dreams. As technology continues to evolve, SLS printing with PA12 is poised to play an increasingly vital role in shaping our world.